Unraveling the Secrets of the Hard Board Production Line
Jun 25,2025
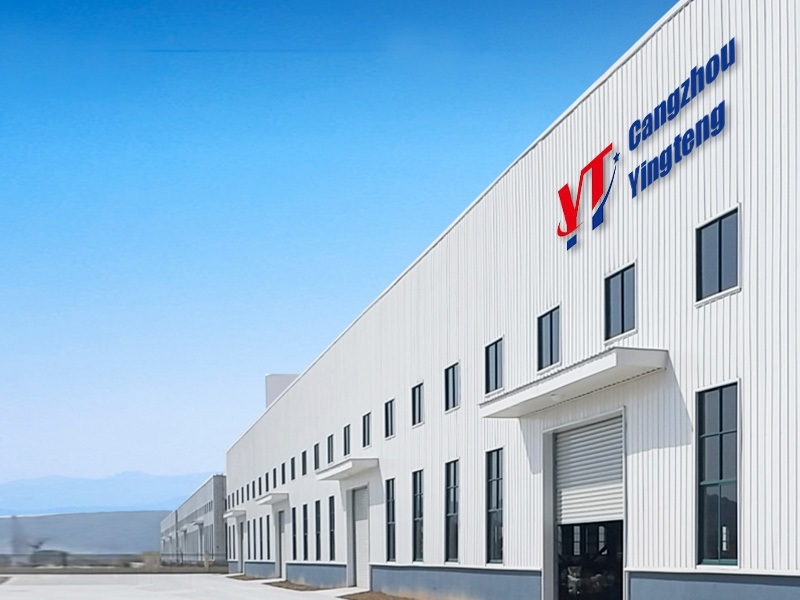
Understanding the Hard Board Production Line
Have you ever wondered how those sturdy hard boards are produced? You’re not alone! The Hard Board Production Line is a fascinating process that combines technology, efficiency, and a touch of artistry. Let’s dive into the nitty-gritty of how it all works!
What’s in a Name?
First off, let’s break it down. A hard board, often referred to as fiberboard, is a dense board made from wood fibers. When we talk about the Hard Board Production Line, we’re essentially discussing the entire assembly line that transforms raw materials into these durable boards. Sounds simple, right? But there’s a lot more than meets the eye!
The Raw Material Dance
At the beginning of any hard board production line, we’ve got the raw materials—wood chips, sawdust, and sometimes even recycled fibers. These materials are the lifeblood of the process. They head straight into a defibrator, where they’re turned into pulp. This is where the magic begins! Imagine a blender on steroids, working tirelessly to break down those wood fibers.
The Pulping Process
Once the wood has been pulped, it’s mixed with water and sometimes additives to improve the board's properties. This mixture is then fed into a refiner, which further breaks down the fibers. At this stage, you might think, “This sounds like a lot of work for a piece of board!” Well, you’d be right! But hold on; we’re just getting warmed up!
Forming the Board
After pulping, it’s time to form the board. The slurry is pumped onto a forming machine, where it’s spread out evenly and squeezed into sheets. Think of it as making a giant pancake, but only much heavier and, well, less delicious! This stage is crucial because the thickness and density of the board begin to take shape.
Pressing and Drying
Next up, we move on to the pressing phase. The sheets are placed in hot presses that apply immense pressure and heat. This not only bonds the fibers together but also removes moisture. You could say this is like giving the board a spa day—relaxation, heat, and a fresh new look!
Finishing Touches
So, what’s next? After the pressing and drying, the boards are trimmed to size and may undergo additional finishing processes. This can include sanding, sealing, and even painting, depending on the product specifications. And voilà! What started as wood chips has now transformed into a hard board ready for use.
Quality Control: The Unsung Hero
Now, let’s not forget about quality control! Before these boards head out the door, they’re thoroughly inspected to ensure they meet industry standards. A good production line won’t compromise on quality—after all, nobody wants a wobbly shelf, right?
The Eco-Friendly Angle
In today’s world, sustainability is key. Many modern hard board production lines utilize recycled materials, reducing waste and environmental impact. This eco-friendly approach not only helps the planet but also appeals to consumers who are increasingly conscious about their purchases.
The Future of Hard Board Production
As technology advances, so too does the hard board production line. Innovations such as automated systems and AI-driven quality checks are becoming commonplace. Who knows what the future holds? Maybe we’ll see boards that are even stronger, lighter, and more versatile!
Conclusion: A Journey Worth Taking
So there you have it! The Hard Board Production Line is more than just machinery; it’s a blend of science, technology, and creativity. Next time you see a hard board, take a moment to appreciate the journey it took from raw material to finished product. It’s a wild ride, and we’ve only scratched the surface!